- Visibility 54 Views
- Downloads 8 Downloads
- DOI 10.18231/j.ijpca.2024.026
-
CrossMark
- Citation
Chemical oxygen generator for emergency use in a resource poor settings: A prototype
- Author Details:
-
Anurag Garg *
-
Ravi Singhal
-
Ritesh Chandra
-
Shyamli Varshney
Introduction
Regular supply of pure oxygen is the need of the hour to be prepared for the fresh waves of COVID-19. The cost of such oxygen supplies should be economical to reach out to the masses & avoid unwelcome burden on the national economy. Although, oxygen concentrators and oxygen plants have been procured in bulk quantities, the raw materials, especially Zeolite are available in limited quantity and may become a choke point for continuous and prolonged use of these equipment.
Another void in effective supply chain of oxygen supply, is the logistics dependency on Oxygen generation plants which are primarily available only near commercial hubs and cities for refilling of oxygen cylinders. Oxygen cylinders have an inherent disadvantage of refilling requirement, huge storage space facilities & continuous gas leaks (almost half the volume) from the cylinders. A requirement has always been felt to identify an alternate source of oxygen generation with readily available raw materials which can ensure its cost effectiveness and last mile oxygen availability through independent generation capabilities .
In 2009, the UK Ministry of Defence, required medical oxygen to be supplied to the casualties on the battle- field and for subsequent evacuation to a forward medical post. [1] The available oxygen generation devices in situ include battery-powered electrochemical devices such as oxygen concentrators and chemical methods like use of ‘oxygen candles’ which worked on the principle of decomposition of hydrogen peroxide and sodium percarbonate in water[2], [3], [4], [5], [6]. But all these methods had few shortcomings and did not fulfill the requirement of continuous & immediate supply of oxygen in emergent situations.
Professors from Swansea University College of Medicine, Swansea, UK had undertaken full- scale experiments to develop a chemical oxygen generator, avoiding using compressed gas, by using a stainless steel vessel, and found that optimum combination of reagents to produce quick constant flow of oxygen, be 1 litre water, 0.75 g manganese dioxide catalyst, 60 g sodium percarbonate granules and 800 g of custom pressed 7.21 (0.28) g sodium percarbonate tablets. This combination of granules and slower dissolution tablets produced a rapid initial oxygen flow to ‘purge’, thus allowing immediate use through a low-flow breathing system, followed by a constant flow for a minimum of 1 h duration.[1], [2]
The authors undertook a task to build up a prototype based on above principle of chemical generation of oxygen , where all the raw materials and components were readily available in bulk.
Aim
With an aim to cater for regular supply of pure oxygen keeping in mind, the future waves of COVID-19 , fabrication of a stand-alone and portable medical grade oxygen manufacturing plant was undertaken to ensure last mile availability of this critical resource in an economically viable, safe to use and ergonomic to operate technique.
Parameters
The oxygen generation plant should be portable for easy transport and installation at remote & inaccessible locations.
The components and chemicals required should be easily available in the local market for mass production.
It should be cost effective for procurement on a large scale.
It should be safe for use by an untrained operator.
The oxygen generated should be of at least 93% purity.
Methods
The prototype was built at a local workshop , observing all standard safety procedures. Clearance was taken from the Regional Ethics Committee. Opinion was sought from technical experts of IISc & BEL Bengaluru and formal review was done for the final evaluation which was conducted off-site.
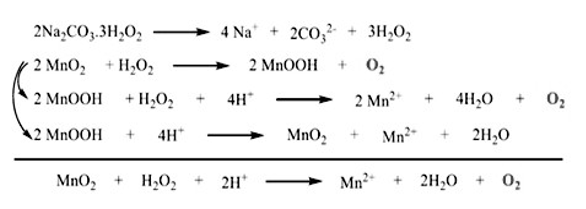
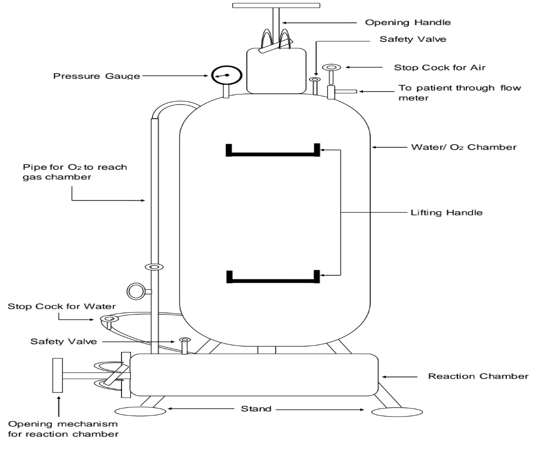
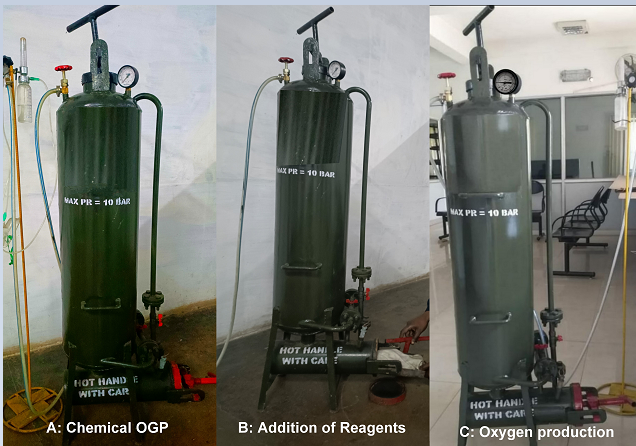
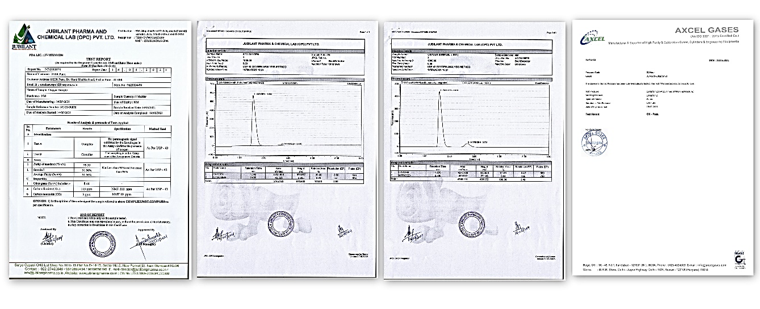
Working Principle
Chemical generation of oxygen has been the go-to technology for portable oxygen generation. This has been extensively used in submarines while operating sub surface levels and in aircrafts, when the cabin pressure drops. However, the cost of production and controlling the reaction has generally been uneconomical for commercial applications.
Our Chemical oxygen generator works on the principle that Sodium per carbonate (SPC), is a loosely held combination of 2 molecules, which dissociates into sodium carbonate and hydrogen peroxide. A catalyst MnO2 is made to interact with this hydrogen peroxide which decomposes further to produce oxygen.(Fig 1)
Fabrication
A cast iron tank with a reaction chamber at the bottom is fabricated for the manufacture of oxygen.
The upper tank consists of water and space for storing gases. The flow of the water is regulated to control the speed of the reaction.
IThe chemical mixture consists of 1:0.015 ratio of sodium percarbonate and manganese dioxide tightly packed in a cloth bag.
A gauge is connected to the top of the tank for measuring the pressure.
Oxygen release valve is kept at the top of the tank which is connected via a pipe to the standard oxygen flow meter to check the quantity of oxygen as well as the oxygen mask for the patient. (Fig 2)
Prototype
This prototype has the main tank volume of about 70 litres with a reaction chamber capacity of 6 cm3, which can hold up to 3 Kgs of reactants at a given time. The entire cost of manufacturing this equipment was $500 (35,000 INR). (Fig 3)
Testing /Validation
The prototype was tested for production of Oxygen, and its purity has been validated at the Global Gas plant and also by gas chromatography technique by IISER and an independent lab. (Fig 4). The points noted were:
The reaction starts instantaneously when the water is released into the reaction chamber. The flow rate of water in the tank is about 150ml/second.
The pressure starts building in the tank in 5-6 minutes after adding water. 3 kgs of reactant required 9 litres of water to produces about 450 litres of oxygen.
Though the tank is capable of withstanding up to 13 bar pressure but, keeping the safety in mind, we kept 10 bar pressure (by using pressure release valve) to get the optimum capacity of oxygen in the tank (600 litres)
The oxygen flow is regulated and controlled to give oxygen at a flow rate of 2 lts/min to 8 lts/min by using a standard oxygen flowmeter connected by high pressure tubing. Flow rate of up to 15 lts/min has also been tested.
The prototype has an inherent capacity of supplying up to 2 hours at 5 lpm and for an hour at 10 lpm.
The reaction was terminated, once the water supply to the chamber is cut off.
Discussion
Readily available supply of pure oxygen is the need of the hour to be prepared for the fresh waves of COVID-19. The cost of such oxygen supplies should be economical to reach out to the masses & avoid unwelcome burden on the national economy. Although, oxygen concentrators and oxygen plants have been procured in bulk quantity, the raw materials especially Zeolite are available in limited quantity and may become a choke point for continuous and prolonged use for this equipment.
There has been a time requirement to cater for emergency medical oxygen supply to remote & resource poor settings. Available mechanisms for generation of oxygen in situ had shortcomings and did not fulfill the requirement of continuous & immediate supply of oxygen in emergent situations.
Our prototype, which has been tested by the standard agencies has tried to overcome most of these limitations. Some of the highlights of this innovation are as follows:
It is Lightweight, can be carried by men with no other infrastructure requirement and no dependency on electricity making it a viable portable solution for ensuring oxygen delivery to the remotest of locations leading the fight against COVID.
The chemicals required are readily available and the bulk procurement of chemicals will drastically bring down the net cost of oxygen generation to about 0.001 USD (Rs 0.66) per litre of oxygen. A tank costs about one third (1/3rd) as compared to standard oxygen concentrators using Zeolite and almost twenty times less than an oxygen generation plant using PSA technology
The oxygen generated has been tested for purity by independent sources using different technologies and the purity has ranged from 91.7% to 97% which are all medical acceptable purity grades.
It is easy to operate and safe to use with inbuilt safety valves to activate in case of excessive pressure.
This device allows for regeneration of oxygen by feeding more chemicals without hindering oxygen flow to the patient.
The reaction takes less than 2 minutes to start and peaks at about 6-7 minutes, generating fresh oxygen within 10 minutes and hence facilitating quick production, thereby minimizing the risk of contamination of gas or leakage or the dangers of transporting a dangerous gas in pressurized cylinders.
The rugged design and easy to use equipment pave the path for self-sufficiency to the remote locations and has the potential to drastically reduce, not only the COVID deaths but also other medical emergencies requiring oxygen administration in the country.
Unlike Zeolite or oxygen, transportation of Sodium per carbonate is safe by air/ road and does not need any other safety measures.
Right from the raw materials (routinely used to make detergents) to the tanks, all items have been indigenously designed and fabricated reducing dependency on imports.
The inherent anti-fungal and anti-bacterial properties of Peroxide further make it an ideal candidate for minimising the risk of Mucormycosis (black fungus).
Limitations & improvements
Improvised Versions of these prototypes with automated water delivery and electronic control for the reaction as well as having inbuilt oxygen sensors can also be produced at added costs.
The temperature in the reaction chamber can reach up to 150 degrees C. The same can be insulated for additional safety of the operator
A stainless steel tank would be more durable and less prone to damage due to oxidation.
Conclusion
A med grade oxygen of 96% purity was produced using chemicals which are available easily in local markets. A cast iron tank was used to facilitate the chemical reaction inside the reaction chamber. The oxygen thus produced could be used by patients who are in dire need of oxygen especially during these trying times of the pandemic.
The main usage of this tank will be to make the remote areas self-sustaining in terms of Oxygen generation and allow timely delivery of oxygen to patients till the time they are taken to the nearest health care facility. This will drastically reduce the mortality at a bare minimum cost.
This equipment, has a definite potential to be the game changing indigenous solution for production of oxygen in the fight against COVID especially in remote and difficult to access areas as well as areas without electricity.
Financial Disclosure
The Authors had privately funded the entire project and did not receive any grant from any organization or corporate.
Source of Funding
None.
Conflict of Interest
None.
Acknowledgements
Technical help and advice from ISRO, IISc, BEL Bengaluru, Prof Sreenivasan of IISER, Pune.
References
- J Dingley, D Williams, P Douglas, M Douglas, JO Douglas. The development and evaluation of a non-pressurised, chemical oxygen reaction generation vessel and breathing system providing emergency oxygen for an extended duration. Anaesthesia 2016. [Google Scholar]
- JA Carter, PJ Basket, PJ Simpson. The ‘Permox’ oxygen concen- trator. Its mode of action, performance and potential applica- tion. Anaesthesia 1985. [Google Scholar]
- L Hall, R Kellagher, K Fleet. A portable oxygen generator. Anaesthesia 1986. [Google Scholar]
- WB Murray, NR Bhimsan, CC Rout. A laboratory assessment of oxygen delivery from a portable chemical generator. Anaesthesia . 1996. [Google Scholar]
- NW Pollock, GW Hobbs. Evaluation of the System O2 Inc Non- pressurized Oxygen Delivery System. Wilderness and Environ- mental. Medicine 2002. [Google Scholar]
- NW Pollock, MJ Natoli. Chemical oxygen generation evaluation of the Green Dot Systems, Inc portable nonpressurized emOx Device. Wilderness Environ Med 2010. [Google Scholar]